MONOCOQUE
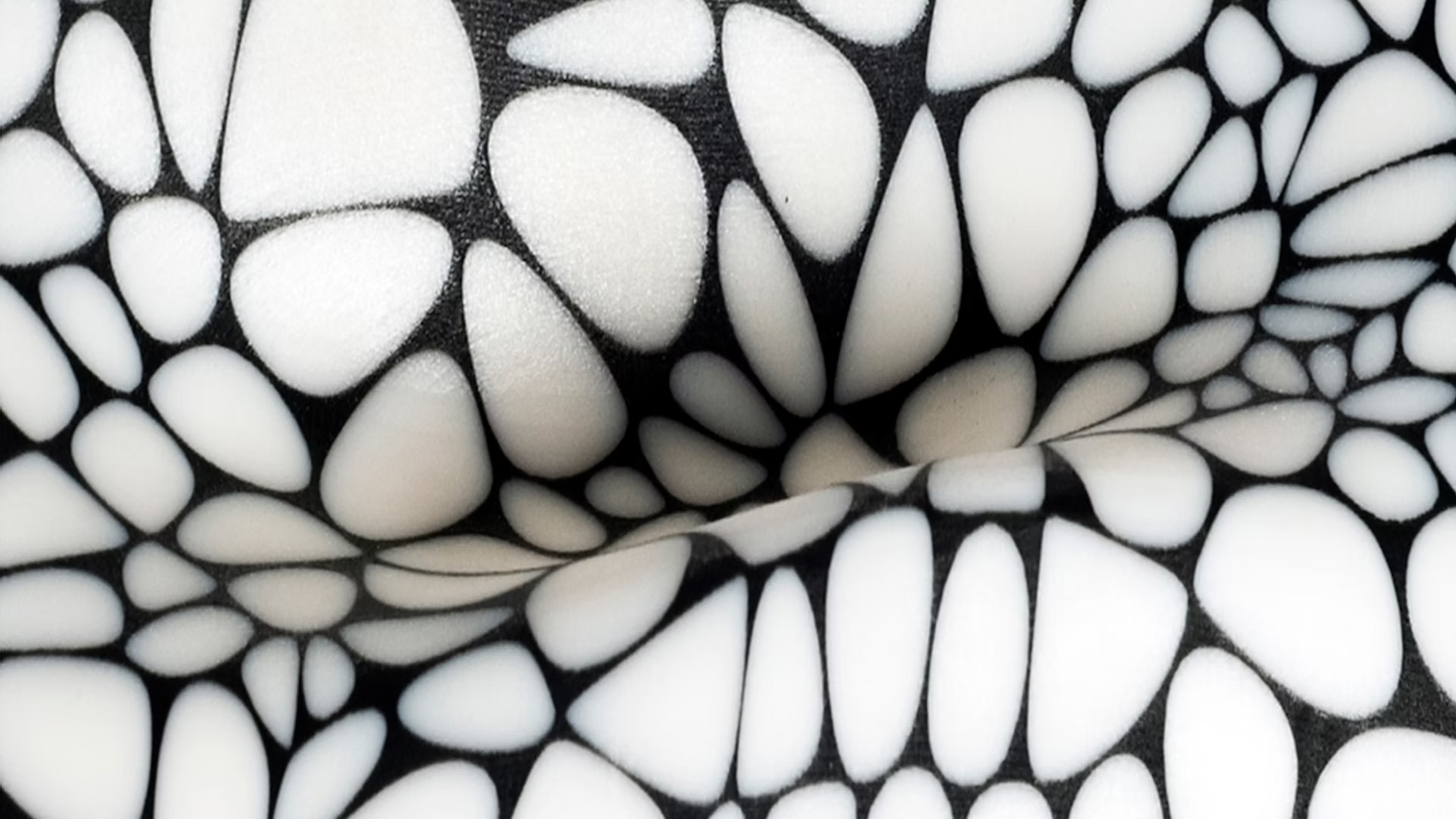
Structural skin
Researcher: Prof. Neri Oxman
Year: 2007
Location: MoMA. Permanent Collection. New York, NY
Process
State-of-the-art technologies are applied here for the first time to cater to a large range of physical properties and behaviors. The surface patches are printed in 3-D, using a new multi-jet matrix technology, which simultaneously deposits materials of different properties. The texture inherits the geometrical features of the design as defined by the user.
By analyzing the structure of the human body and where pressure is concentrated, the chaise becomes softer and more flexible at points where tension needs to be relieved, and stiffer where more support is required. The relative volume of each cellular cushion is locally informed by pressure data averaged with values that represent structural support and flexibility. Global and local mean curvature values inform its density, such that denser, smaller cells are organized in areas of steep curvature, and larger cells are found in areas of shallow curvature.
Project
Monocoque embodies a design and digital fabrication process producing structures that support load using their own external skin. Contrary to the traditional design of building skins that distinguish between internal structural frameworks and non-bearing skin elements, this approach promotes heterogeneity and differentiation of material properties.
The project demonstrates the concept of a structural skin using a Voronoi pattern, the density of which corresponds to multi-scalar loading conditions. The vein-like elements that are built into the skin distribute shear stress and pressure over their surfaces. The innovative 3D printing technology used in this process enables designers to print parts and assemblies made of multiple materials within a single build. It also enables the creation of composite materials that present preset combinations of mechanical properties.
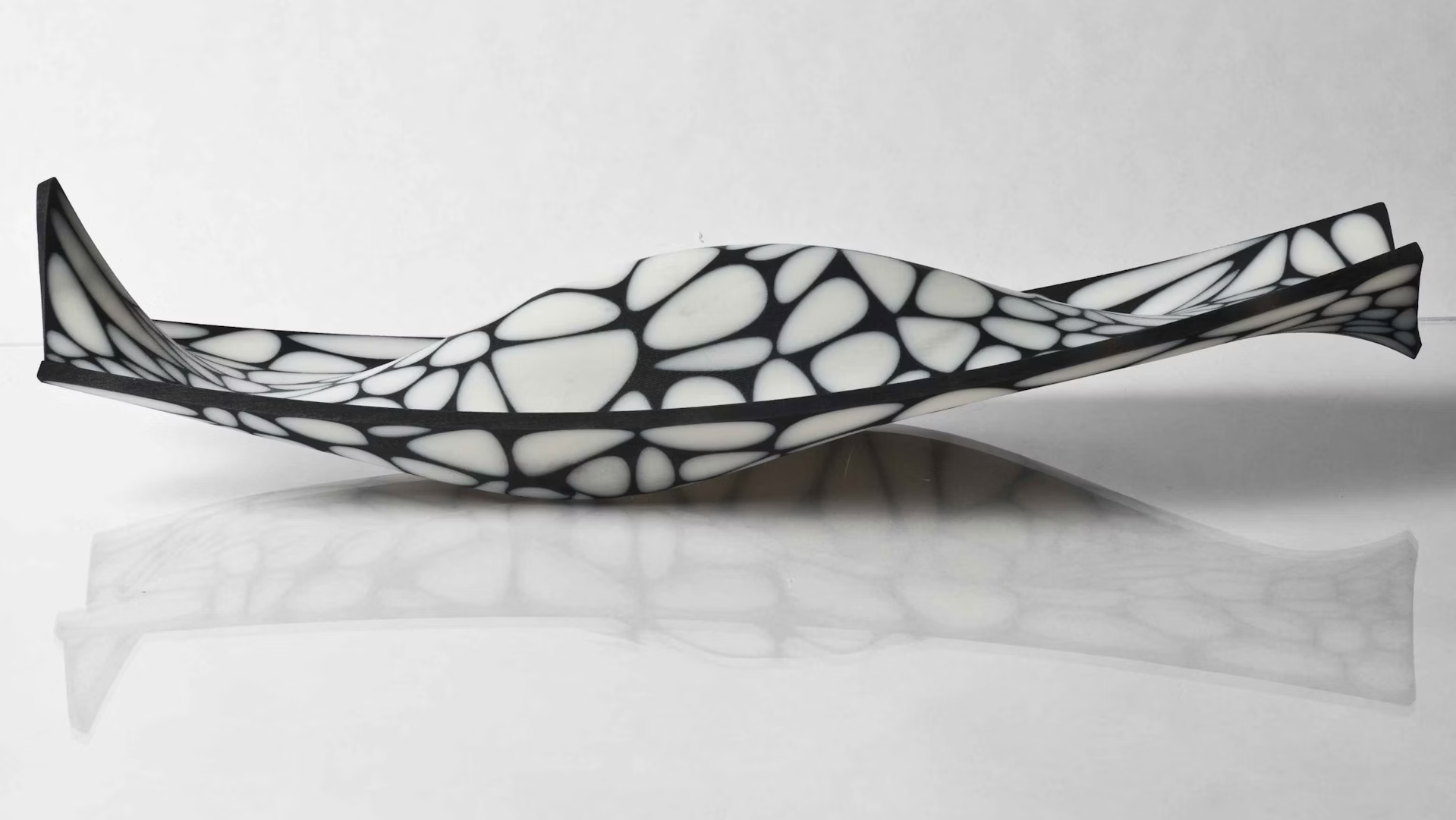
Credits
Collaborators & Contributors: Stratasys Ltd., Z-Corp
All images and videos courtesy Neri Oxman