O°
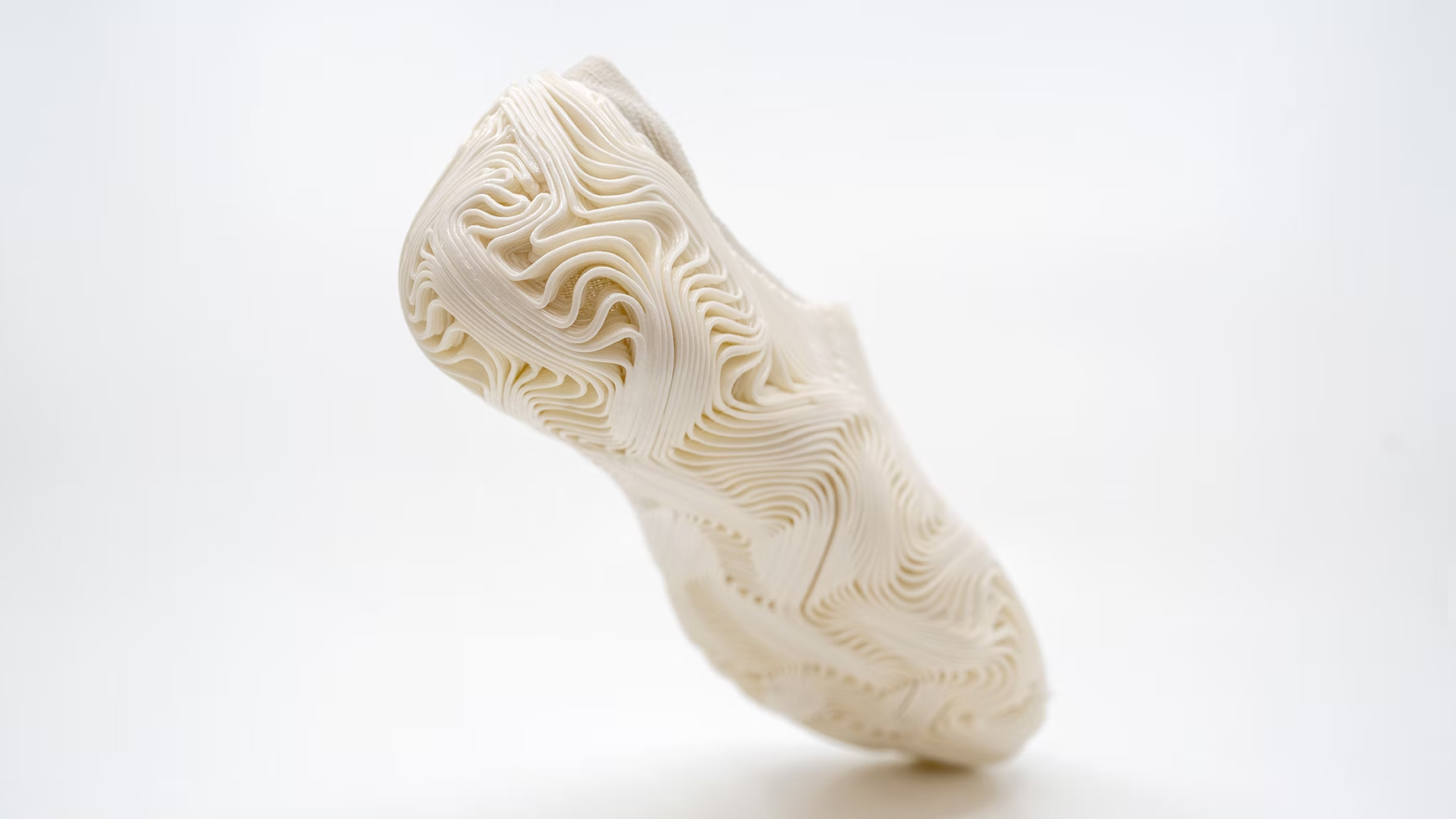
From bacteria to bacteria
Can products grow and decompose as ecosystems? Can we design the life cycles of consumer goods to borrow matter and energy from Nature and return them upon obsolescence? We present a revolutionary class of biologically programmed, computationally grown, and robotically manufactured shoes and textiles that give biodegradable bioplastics the design that their biology deserves.
Research team: Christoph Bader, Florian Born, Sarabeth Buckley, David Franck, Markus Kayser, Nic Lee, Anran Li, Zane Lindstrom, Jessy Lu, Neri Oxman, Luis Soenksen, Finn Stirling, Tim Tai, Marcus Walker, Leila Wallisser, Andrea Westlie
Made entirely of polyhydroxyalkanoates (PHAs), a bacterially produced thermoplastic polymer, the mono-material Oᵒ platform enables the design and digital fabrication of apparel items, such as shoes and textiles, that exhibit a range of physical properties, functions, and end-of-life trajectories. Since PHA-producing bacteria can utilize a variety of feedstocks the products designed with them can lead to a range of carbon footprints. In addition, we process PHAs using various digital fabrication methods —from 3D printing to hot melt spinning and knitting. Such high levels of versatility, achieved through design tunability across design stages and media—production, processability, and programmable decomposition— are at the core of Oᵒ’s designs and platform technology.
The Oᵒ platform embodies a world where design and digital fabrication are vertically integrated with biomaterial production systems to achieve programmable decomposition of goods designed for the mutual benefit of ecosystems and the environments around them.
By exploring synergies across scales and disciplines—from synthetic biology to green chemistry, materials engineering, design, and computation—we aspire to create products and processes that rekindle the relationship between the ‘grown’ and the ‘made’ in thoughtful, useful, and meaningful ways.
Position
Fashion and product design embody significant environmental impact. From energy-intensive manufacturing of petroleum-based materials to ineffective strategies for end-of-life disposal, these industries pollute our air, our water, and our soil. Microplastics containing ‘forever chemicals’ are among the key culprits, infiltrating our bodies and planet, and exacerbating the interconnected issues of social and climate injustice.
In place of assembling independently produced parts, each with its homogeneous material properties, we harvest biological mono-materials with highly tunable properties to create gradients of functionality.
tons of garments that end up discarded annually
Platform
The O° platform is composed of tools, techniques, and technologies in the areas of biopolymer engineering, fiber production, and processing; as well as performance-driven computational design, knitting, and robotic fabrication.
The most impressive material systems in the natural world often achieve their performance by making small modifications to a single, versatile material. Cellulose, for example, comprises over half of all plant matter, from rigid heartwood to flexible leaves. Similarly, chitin adapts to both the tough shells of crustaceans and the transparent wings of dragonflies. This focus on adapting versatile, abundant building blocks allows Nature to achieve unrivaled performance and sustainability.
Meanwhile, human systems formed from over-engineered amalgamations of diverse materials with different strengths, weaknesses, and life cycles struggle by comparison. The construction and separation of materials contributes to manufacturing waste that causes environmental and personal harm.
In contrast, the Oᵒ platform aims to leverage a versatile mono-material system tuned to deliver a wide array of mechanical, thermal, chemical, and manufacturing properties that meet a broad range of processing needs and applications. It offers fundamental advantages for manufacturing and end-of-life strategies in a vertically integrated approach to biopolymer design, digital fabrication, and programmable decomposition. An Oᵒ consumer product can be produced in its entirety in a single location, on a single material class, using a single fabrication system.
Platform Details
In Oᵒ, we work with polyhydroxyalkanoates (PHAs)—a highly versatile material naturally produced and decomposed by bacteria—and tune their mechanical and chemical properties to be suited for a broad range of industrial applications. Oᵒ products celebrate the versatility of PHAs by incorporating them across a myriad of technical material challenges.
The current world of plastics fills numerous material niches, due to the immense variety and tunability of physical properties. Replacing non-biodegradable, petroleum-based plastics requires developing and producing alternatives at scale, applying them to diverse structures that expand the material’s potential use cases.
As a biologically recyclable material class, PHAs offer promising alternatives to petroleum-based plastics. Considered one of the only biologically derived thermoplastics, they are easily integrated into most industrial manufacturing processes, including melt extrusion, injection molding, melt blowing, fiber spinning, and casting.
At OXMAN, we are engineering novel PHAs and PHA blends for consumer applications that span life and afterlife, positing the notion that a product is equally useful for Nature-centric means on the other side of its human-centric use. Since PHAs are easily biodegradable in marine and soil environments, we ‘program’ timed decomposition into the product, empowering its user to consider the carbon sources used to create it, and the process—time, place, and movement—by which it can be dissociated.
Several wild and engineered microorganisms demonstrate a natural ability to produce PHAs from abundant carbon sources (e.g., carbon dioxide, methane, glucose, and waste streams) and store them in cytoplasm as intracellular carbon and energy reserves.
OXMAN is conducting directed evolution, metabolic engineering, and strain selection studies to evaluate two model organisms as potential bacterial coproducers of PHAs for consumer applications, optimizing for low energy input requirements, high material yields, and carbon neutrality or negativity.
In the realm of textiles—including weaving and knitting—O° biomaterials are well-suited for fiber development.
Industrial textile fabrication processes are often very aggressive to fibers, necessitating resistance to snapping and stretching, among other attributes. Maintaining adequate tenacity and elasticity such that this fiber can be subject to textile manufacturing processes requires intensive research and development.
At the cutting edge of material science, microbiology, and engineering, our team is currently developing mono- and multi-filament fibers using biologically produced PHAs, with a focus on increasing tensile strength to rival that of commercial synthetic fibers.
We extrude PHA in long continuous fiber filaments as long as tens of thousands of meters and as small as 30 microns in diameter, with robust mechanical performance across a limited cross-sectional area. In addition to pre-production runs of biodegradable PHA-based mono- and multi-filament fibers, we have achieved successful production runs of 100% PHA fibers.
We transform fibers into textile products using CNC knitting, an industrially scaled textile fabrication method that has existed for decades. Unlike most machines in our lab, this machine is not custom, or of our own invention, but rather the same kind that already exists in manufacturing on the factory floor.
The knits act as the ‘musculature’ for our products, providing a robust substrate that connects ‘exoskeleton’ (i.e., 3D printed elements) and ‘fat’ (i.e., melt-blown elements). It coheres the 3D printed lines in areas where coverage is needed and flexibility is desired.
Interlacing fibers to create shape and movement enables us to computationally ‘grow’ geometries from a single thread. As a result, our 3D knitting technology is close to a zero-waste process.
OXMAN has developed novel fabrication methods for custom PHA blends, including melt spinning industry-grade fibers, fused deposition modeling of 3D printed filaments, melt blowing nonwoven textiles, and molding foams. We introduce them here in the context of creating one of the most challenging wearable products to manufacture: a shoe.
We transform fibers into textile products using CNC knitting, an industrially scaled textile fabrication method that has existed for decades. Unlike most machines in our lab, this machine is not custom, or of our own invention, but rather the same kind that already exists in manufacturing on the factory floor.
The knits act as the ‘musculature’ for our products, providing a robust substrate that connects ‘exoskeleton’ (i.e., 3D printed elements) and ‘fat’ (i.e., melt-blown elements). It coheres the 3D printed lines in areas where coverage is needed and flexibility is desired.During melt blowing, hot air jets out nanoscale filaments of melted PHA. Fine fibers are dynamically distributed and cooled into a seamless nonwoven textile. Melt-blown PHA can augment foam as a cushioned material base, offering exciting opportunities for bio-based footwear design, apparel, and beyond.
Depositing layer upon layer of material, our custom-built 3D printer gives rise to functional and aesthetic topography through a single continuous line. While most layer-by-layer 3D prints in the shoe and additive manufacturing industries occur on a flat print bed, we introduce a novel method that occurs in non-planar motion and eliminates the cut-and-sew and adhesion processes of a traditional assembly line.
Interlacing fibers to create shape and movement enables us to computationally ‘grow’ geometries from a single thread. As a result, our 3D knitting technology is close to a zero-waste process.We use a 3D printing method called fused deposition modeling (FDM), wherein an extruder melts down PHA pellets into a malleable fluid, called a filament. At the end of a robotic arm is a last in the shape of a human foot—the starting point of any shoe construction. In a programmed dance, these components sequentially perform additive manufacturing on top of a sock-like textile. We call the 3D printed layer our shoe’s ‘exoskeleton,’ as the PHA copolymers provide material toughness, while the designed toolpath of the continuous line provides mobility and flexibility.
This programmed fabrication is what we call ‘toolpathing,’ or the output of intensive computational design processes for the robotic arm to enact. The toolpath can be quickly iterated, closing the gap between design and manufacturing to unify them as one.
We are in parallel exploring using automated spatial calibration with a standalone CNC machine to replace the robotic arm, allowing us to significantly increase speed and precision while shrinking the overall footprint of the system. With the development of a custom 5-axis 3D printer, we transition from a generalized robotic approach to an application-specific scalable system. Our goal is to create a machine that is both fast and precise, ensuring that the only design constraint is the physical limits of the materials.
To support this next-generation machine, we are building an adaptable platform designed to seamlessly integrate additional processes. This system is based on state-of-the-art industrial components and standards, enabling its incorporation into existing factory and even retail environments. Combined with a robust safety system, these standards lay the groundwork for UL or CE certification.
Product
We present the first-ever Nature-centric shoe and apparel line, made with 100% biodegradable PHAs. Designed for sustainability, our products break down in most natural environments, leaving zero microplastics behind. This biological material platform provides a wide set of options for future-efficient carbon and energy utilization during synthesis, as well as genetically and chemically encoded pigmentation and novel material properties.
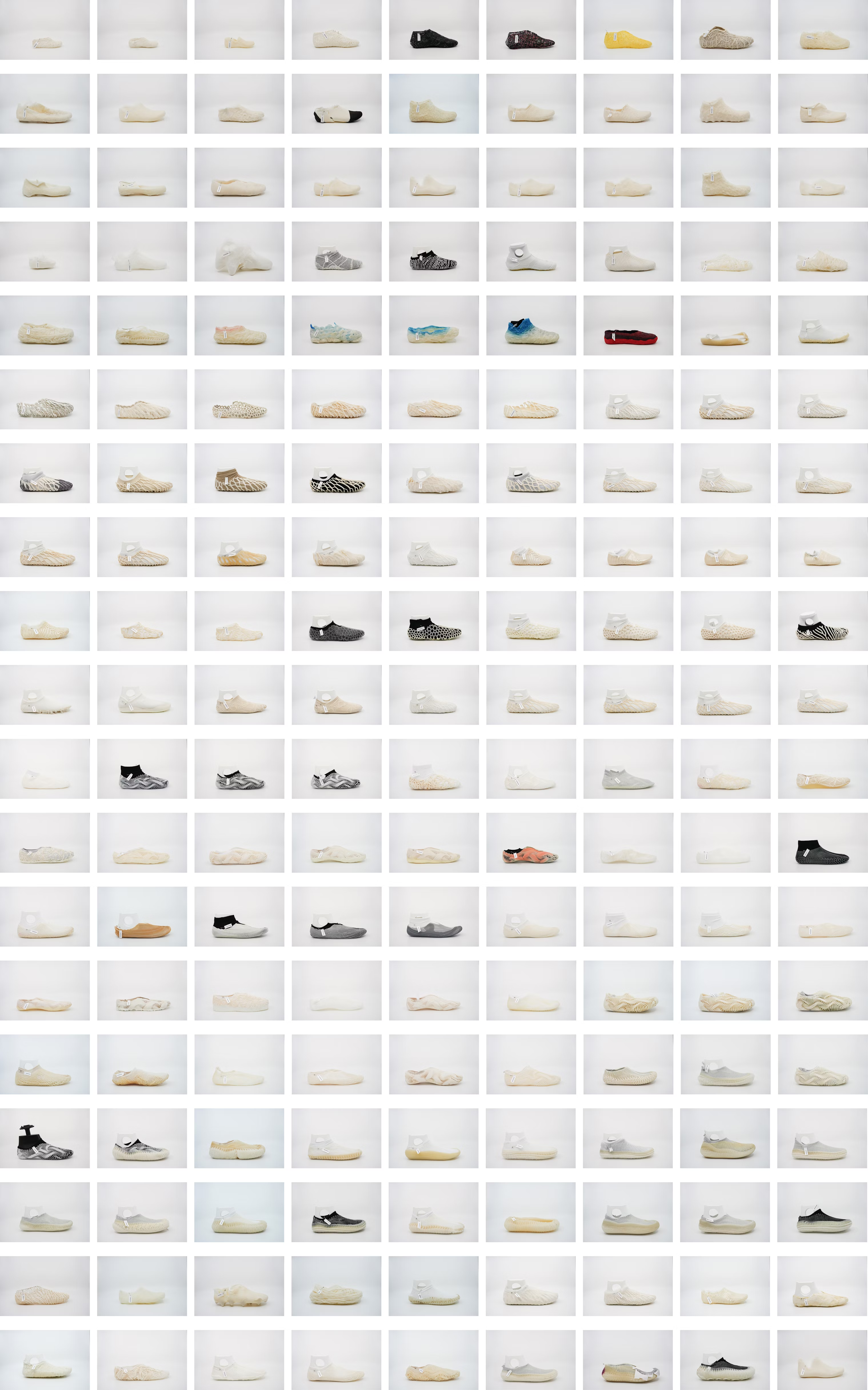
NO. OF MATERIALS USED TO CREATE A TRADITIONAL SHOE
Materially, a shoe represents manifold functions, from comfort to performance, from ergonomics to aesthetics; it is our most constant touchpoint with the physical world.
With circa 40 distinct materials and associated fabrication methods involved, a shoe is also a particularly challenging topology to design and manufacture. A typical shoe can be considered an assembly of materials and chemicals that exhibit a range of performance attributes patterned to accommodate the function and comfort of a highly complex biomechanical system: the human foot.
The foams, fabrics, rubbers, coatings, and adhesives each represent a product category that requires its own energy-intensive chemical and process development, as well as factories for production at scale. These diverse components must be assembled and adhered to each other, often with synthetic glues, to create a product that humans consume billions of per year¹.
RANGE OF "FOREVER CHEMICALS" IN A TRADITIONAL SHOE
There are notable environmental and ethical implications of the mass-market shoe—a consequence of a highly globalized supply chain, chemical formulations that are hazardous to both workers and the environment, and no clear end-of-life for a multitude of materials that cannot be recycled or biodegraded.
O° aims to remove the complexity involved in the fabrication of objects by tuning a single and versatile mono-material class known for its biodegradability in ambient conditions and its ability to be produced from feedstocks such as atmospheric carbon dioxide or methane². Streamlining manufacturing allows us to remove externalities that would incur environmental damage; if we only need one material to make a shoe, we have no need to import specialized components from around the globe. Reducing microplastics, reducing atmospheric greenhouse gases, and promoting biological growth through targeted biodegradation follow as further vectors of positive environmental impact.
The O° shoe is not a single shoe design but a design language and potential world of shoes made from PHA. It embodies the versatility of PHAs by incorporating them as knitted textiles and tough 3D printed elements in precise designs informed by the kinetics of human motion and requiring strict standards for comfort, robustness, and aesthetics.
At the heart of each shoe is a unifying base layer of a knitted sock. Given the shoe’s individual intent (e.g., ballet slipper, sneaker), outer layers are printed on the knitted textile to provide specific functionalities such as reinforcement, cushioning, strength, and pliability. The versatility and automation built into the O° platform technologies enable rapid iterations and an accelerated development process from design to production.
Platform Details
Each design is generated and evaluated as a series of ‘toolpaths’ or continuous curves, in an iterative feedback loop. By gradually transforming single curves in 3D or by applying graph theory to discover single-curve toolpaths, a wide variety of functional solutions is generated within a given design space.
With continued integration of the computational design tools described above, we strive to weave a more profound link between the predictive modeling of textiles and gradient mechanical behavior. The exploratory use of 3D model-to-knit software introduces the ability for our team to parameterize knit designs for increased complexity across functional and mechanical attributes as well as in shape and construction.
Many industrial pigments and dyes are sourced from petrochemical feedstocks, are implicated in the release of environmentally damaging chemicals during their production and usage, and are dependent on a resource intensive and complex global supply chain for synthesis, processing, and transport.
In contrast, biological systems can generate pigments from simple and abundant feedstocks such as sugars, waste food streams, and even carbon dioxide and methane, in temperate conditions through enzymatic processes. O° explores the engineering of bacteria not just as a source of material but also to encode other functional properties, such as pigment production, in order to simplify and centralize the manufacturing process.
In natural biological materials, such as our hair and skin, the production of pigments is located at the site of material production. For instance in hair growth, keratin (the main structural protein in hair), is co-produced alongside melanin, the pigment molecule that gives hair its color.
This contextualization of pigment production into the 3D structure of a biomaterial allows for spatial pigment patterning based on DNA-encoded processes, in-situ pigment production that responds to environmental conditions (like skin tanning), and minimal pigment waste, as all pigment is captured within the final biomaterial. O° explores how, through synthetic biology, we can apply these biological approaches to elevate how we manufacture, use, and discard manmade objects.
Oᵒ—zero to the power of zero—stands for one: the first natural number, numeral, and glyph, expressing notions of ‘prime’ and ‘unity’ or ‘union.’ It also expresses the singular nature of its physical embodiment: one bacterial type, one material, one machine, one location, one transformation, and one genetic code.
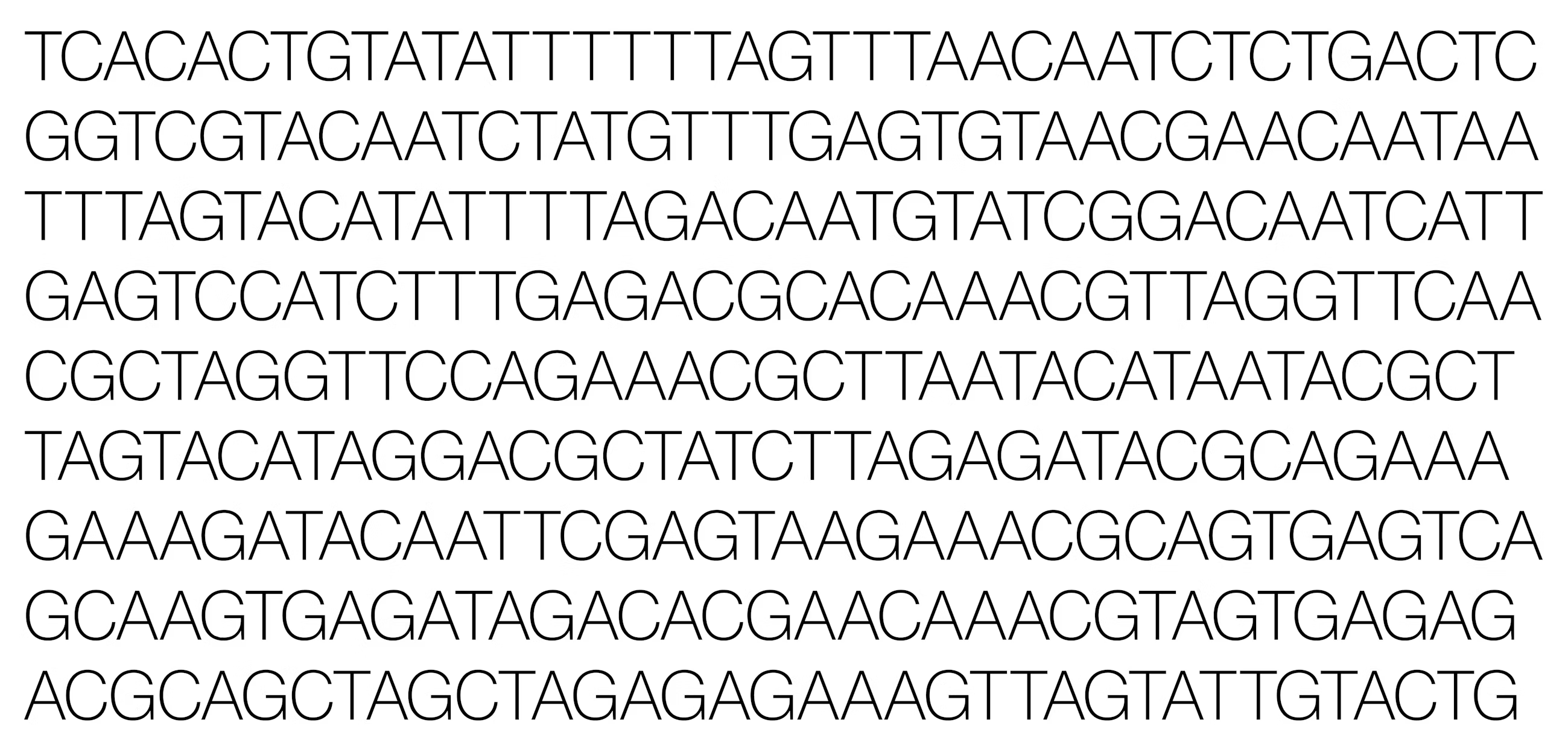
In addition to the physical and chemical properties encoded into the bacterial DNA generating the shoe and the textiles—ductility, pigmentation, and smell—the Oᵒ brand can encompass genetic DNA encoding the project’s brand on PHA-based thermoplastic polymers.
The genetic label of Oᵒ is synthesized in DNA. Once embedded, specific assays—such as PCR —can be used to detect and read the genetic code following polymer biodegradation. This can enable a future where precise identification of disposal and biodegradation of products is an everyday reality.
Genetically encoded labeling in products containing thermoplastic polymers can be designed to carry consumer-facing information such as instructions, messages, and serial codes. It also provides for enhanced traceability: the labels enable traceability throughout the lifecycle of the plastic product, from production to disposal. This can help manufacturers track the source of materials and ensure compliance with regulatory standards. The unique genetic sequences used in these labels can also serve as anti-counterfeiting measures—ensuring the authenticity of plastic products and protecting intellectual property.
Genetically encoded labels for thermoplastic polymers represent a cutting-edge approach to improving the branding and traceability of biodegradable plastics. By embedding molecular information directly into products, these labels may offer fresh value propositions associated with exclusivity, personalization, end-of-life traceability, and security.
Praxis
Lorem ipsum dolor sit amet, consectetur adipiscing elit, sed do eiusmod tempor incididunt ut labore et dolore magna aliqua. Ut enim ad minim veniam, quis nostrud exercitation ullamco laboris nisi ut aliquip ex ea commodo consequat. Duis aute irure dolor in reprehenderit in voluptate velit esse cillum dolore eu fugiat nulla pariatur.
Lorem ipsum dolor sit amet, consectetur adipiscing elit, sed do eiusmod tempor incididunt ut labore et dolore magna aliqua. Ut enim ad minim veniam, quis nostrud exercitation ullamco laboris nisi ut aliquip ex ea commodo consequat. Duis aute irure dolor in reprehenderit in voluptate velit esse cillum dolore eu fugiat nulla pariatur.
By cultivating materials from bacteria, as opposed to extracting them from resources like oil, or sourcing them from farmed materials such as wool and cellulose, we unlock the potential for a radically new production paradigm—one that bears more resemblance to growing than to the conventional manufacturing processes. This approach envisions centralizing all components of production into a single site and process. It is possible to conceptualize a single production process, whereby inputs like gaseous nitrogen and CO₂ are transformed, and on the output side, fully designed materials emerge. This innovative method could be viable both on Earth and in space.
One reason for selecting PHAs as the initial material system for O° is their potential to be carbon neutral or carbon negative. Because PHAs can be produced from a broad range of feedstocks, their production system ultimately determines the material’s carbon footprint in a conventional sense. Life-cycle assessments have reported PHAs manufactured from crop sugars as having carbon footprints between 1.7 and 11 kgCO₂e/kg³. There is a broadening scientific consensus that PHAs can be produced in bulk from atmospheric carbon⁴ and other sources that provide it with a very small or even negative carbon footprint³.
PHA, essentially a bacterial fat, represents a high-calorie food source for certain bacteria and fungi. As a carbon rich food source, it can drive increased microbial growth in the soil ecosystems it enters and unbalance the ecosystem. The challenge therefore is to figure out how to manage the carbon contained in the PHA once the material enters, and then leaves the hands of consumers.
The circular nature of O°—being produced and consumed by the same class of organisms—points to a future where products biodegrading into microorganisms can nourish the soil from which they originate; a future where products can reincarnate into plant matter, and vice versa.
Credits
Consultants: Shoe Design: Nick Daiber; Robotics: Robin Godwyll; Industrial Design: Che-Wei Wang; Microscopy: James Weaver; Software: Christian Kokott
Acknowledgements: Photography: Nicholas Calcott; Videography: Brennan Freed, Eyal Bau Cohen, Alejandro Lazare, Matthew Marino; Dance: Omri Drumlevich, Zina Zinchenko; Soil Expert: Larry Foglia
All images and videos courtesy of OXMAN
Sources
92M
Tons of garments that end up discarded annually
Kumar, J., Singha, K., Pandit, P., Maity, S., & Ray, A. (2020). Challenges for waste in fashion and textile industry. In P. Pandit, S. Ahmed, K. Singha, & S. Shrivastava (Eds.), Recycling from Waste in Fashion and Textiles (1st ed., pp. 19–32). Wiley. https://doi.org/10.1002/9781119620532.ch2
40
Average number of materials used to assemble shoe
Kannaraya, P. S., Dilip, S., Deshpande, C. S., Arora, M., & Chakrabarti, A. (2021). Smart multi-material weight tracking resource bin. In A. Chakrabarti & M. Arora (Eds.), Industry 4.0 and Advanced Manufacturing (pp. 65–74). Springer Singapore. https://doi.org/10.1007/978-981-15-5689-0_7
33-4,200
Range of “forever chemicals” in average shoe
Wolverine Worldwide product testing report. (2019). Ecology Center. https://www.ecocenter.org/sites/default/files/2022-11/WolverineProductReport_Final.pdf.
3
Yates, M. R. & Barlow, C. Y. Life cycle assessments of biodegradable, commercial biopolymers—A critical review. Resources, Conservation and Recycling 78, 54-66 (2013).
2
Yañez, L., Conejeros, R., Vergara-Fernández, A. & Scott, F. Beyond intracellular accumulation of polyhydroxyalkanoates: chiral hydroxyalkanoic acids and polymer secretion. Frontiers in Bioengineering and Biotechnology 8, 248 (2020).
Bhola, S. et al. Established and emerging producers of PHA: Redefining the possibility. Applied Biochemistry and Biotechnology 193, 3812-3854 (2021).
1
Cheah, L., Ciceri, N.D., Olivetti, E., Matsumura, S., Forterre, D., Roth, R. and Kirchain, R., 2013. Manufacturing-focused emissions reductions in footwear production. Journal of cleaner production, 44, pp.18-29
Bodoga, A., Nistorac, A., Loghin, M.C. and Isopescu, D.N., 2024. Environmental Impact of Footwear Using Life Cycle Assessment—Case Study of Professional Footwear. Sustainability, 16(14), p.6094.
4
Bedade, D. K., Edson, C. B. & Gross, R. A. Emergent approaches to efficient and sustainable polyhydroxyalkanoate production. Molecules 26, 3463 (2021).